Fritz Byle discusses high-performance starter contactor design
Sometimes referred to as a starter solenoid, a starter relay is used to switch the high current needed to turn the starter motor on an internal combustion engine. The starter relay comprises a set of high-current contacts and a linear actuator (solenoid) to move one or more of the contacts to make or break the circuit (Fig. 1). 50 Amp Automatic Transfer Switch

When actuated, the solenoid armature moves to the right, removing the spring-applied force that keeps the contacts open, closing the circuit. When de-energised, the solenoid return spring reapplies the opening force, opening the circuit.
Market changes, such as the need for start/stop functionality, are requiring improvements in starter relay performance – namely a much longer operating life (more operating cycles). High-compression engine designs may require higher currents for starting. These changes challenge existing high-current contactor designs. Contact degradation speeds up dramatically as current is increased. The resulting debris can affect mechanical operation of the switch, limiting component life.
Starting current is highest immediately upon closure. This inrush current peak can be more than five times the steady-state current during the start sequence. The advent of higher-compression over-square engines (bore larger than stroke) raises the torque that must be delivered, and therefore the current. Lightweighting has resulted in changes to the configuration of starting systems to remove excess cable length and reduce overall resistance of the starting circuit outside of the motor. Reduction of this series resistance raises the peak current. In one case, inrush current for a 1.3-litre ICE reached more than 900A, a value 50% higher than expected for the starting system. It was discovered that the main driver for the high inrush current was the low series resistance.
High inrush current also drives the risk of contact welding. During high-current closure, there is always some contact welding due to arcing and contact bounce (see Fig. 2 on following page). If enough melted area is present when the contacts close, the weld formed may be strong enough that the contacts will not open when the contactor is released. Raising the inrush current dramatically increases the risk of this dangerous failure mode.
In Fig. 2, the red trace is the current in the starter motor circuit. The blue trace is the solenoid current (right-hand scale). At point (1), the solenoid is actuated. First contact is made at (2), and starter current begins to rise. At (3) and (4) contact is momentarily lost due to bounce. At (5) the solenoid armature has completed travel and is locked to the pole. At (6) the solenoid voltage is removed, and current falls rapidly. Once the magnetic field has decayed, the armature moves back toward its starting position, and at (7) the contacts are opened.
Vehicles using start/stop engine operation require up to 10 times the contact lifetime of non-start/stop vehicles (roughly 300,000 lifetime operations vs 30,000 operations). With high inrush current placing downward pressure on contact life, and start/stop operation requiring dramatic improvements, starter solenoid designs for modern applications face serious challenges.
Existing electromechanical contactors used in automotive applications will typically handle the high inrush currents without failure due to contact welding. However, the resulting contact lifetime is short, and mechanical failure of the actuator often results from the generation of large amounts of metal debris. This results in two predominant failure modes: debris (mostly melted copper particles) mechanically jams the contactor; contact wear is so severe that the contactor can no longer close.
The existing contactors studied had masses of between 350g and 750g. None of these contactors were able to achieve 30,000 cycles with an inrush current of 950A.
Target performance specifications for a high-current contactor capable of operating in start/stop mode for a high-performance ICE would include the following: inrush handling of 950A; steady-state current handling of 200A; contact and mechanical lifetime of 300,000 to 500,000 closures; mass of less than 350g.
Contact material and geometry are the keys to achieving long contact life and high inrush handling. The materials of the mating contacts in automotive solenoids are usually pure copper. High contact life and high inrush handling need a material that would limit the arcing damage, reducing wear and debris. Such materials have the effect of increasing contact resistance. Increasing resistance would imply an increase in the heat generated within the relay, so this needs to be considered.
The internal resistance of the relay is dominated by the contact resistance. In testing of the high-performance contact materials, a 150% increase in contact resistance was noted, which implied an increase of 150% in dissipated power. Fig. 3 shows the internal power dissipation as a function of steady-state current for various internal resistances. The typical contact resistances for copper and high-performance composite contacts are shown. At 200A current draw, power dissipated rose from 16W to approximately 26W.
Of greater concern was the heat generated during the inrush spike. Resistive heating increases as the square of the current. An inrush current of 950A across a resistance of 0.62milliohms generates 560W of resistive heating. The very short duration of this spike was found to contribute less than 1% of the dissipated heat energy over a two-second start cycle, therefore inrush heating was not found to be a significant factor in this specific design.
Evaluation of contact wear for the composite material versus copper was conducted using 950A inrush current and steady-state current of 180A. The contact life of the composite contactor was estimated to be >250,000 cycles.
The lifecycle of the tested contacts was therefore in the range required for start/stop operation while handling the very high inrush currents in a lightweighted system. Debris generation was dramatically reduced (>95%), but for long-life contactors, debris management tactics would be desirable.
With contactor failure modes adequately addressed, solenoid mechanical life becomes the limiting factor in the lifetime of the starter relay assembly. Low-cost solutions used for non-start/stop applications generally do not have the mechanical life for start/stop operation, however mitigations such as lubrication can dramatically improve performance. The cost penalty for a properly implemented solution is typically moderate, about 5% to 10% of the total cost of the contactor.
A final challenge for modern starter relays is lightweighting. High-current relays have masses ranging from 300-750g, with 350-400 being typical. Targets for lightweighted designs were roughly 50% of these masses.
A customer required a starter contactor needing the following key characteristics: 950A inrush handling; 175A steady-state current handling; 30,000 cycle durability; 1m/5 minute water immersion survival; replace an incumbent part weighing 120g.
The incumbent part failed due to contact welding at inrush currents above 600A and had no water immersion protection. It used a copper contact system, and the high-risk failure mode of contact welding was realised during early testing with the actual powertrain. Development of an improved contactor to meet the requirements while maintaining a minimum part mass was undertaken.
The resulting design (see image on previous page) entered production in mid-2020 in an on-road recreational vehicle. The mass of the design is less than 160g and meets the target performance requirements. Current-handling performance meets or exceeds the specification of contactors weighing more than four times as much.
Fritz Byle is senior project manager at TLX Technologies
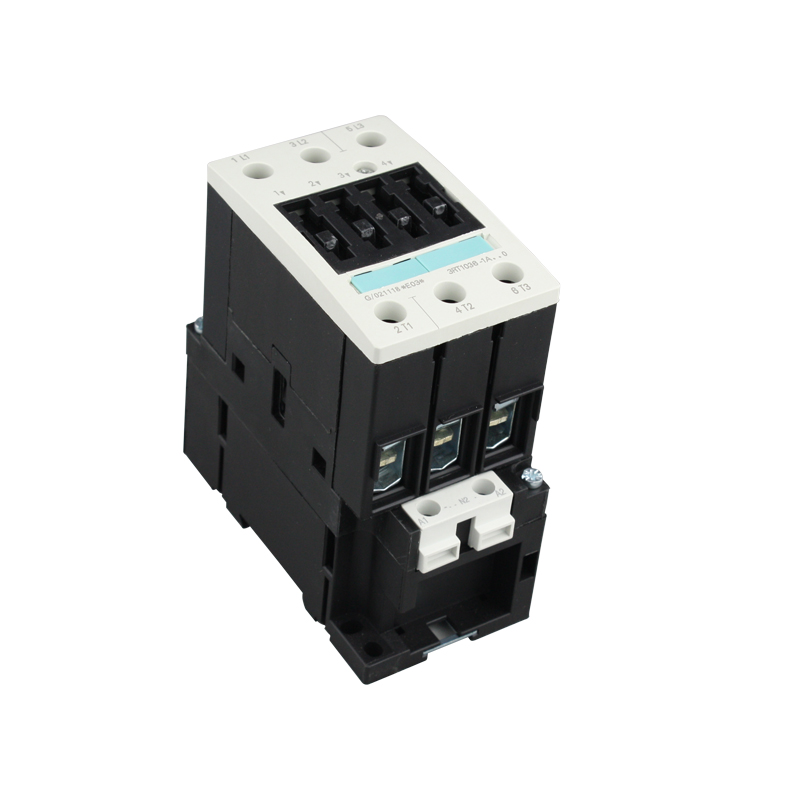
Mccb Full Form © Setform Limited 2019-2024 | Privacy policy | Archive