Armor tensioned screens are built from high-grade wire cloth with molded open-cast premium polyurethane, according to Durex Products. The unique combination produces a screen that has a much higher open area than conventional polyurethane screens, the company says – plus longer wear life than wire screens. Additionally, the tapered design reduces plugging and increases throughput. Combined with a high-grade woven-wire backbone, Durex says the result is a strong, highly wear-resistant screen for light- to medium-load applications with highly abrasive wear. Armor screens are installed just like wire screen panels, so screen boxes for tensioned screen media require no modifications.
Buffalo Wire’s modular PFX/HT hybrid screening panel aims to address open area, heavy loading and throughput issues caused by all-synthetic screen systems. This is achieved by embedding high-efficiency, self-cleaning screen technology into a polyurethane frame system. There is no deck modification required, and it is ideal for heavy-duty applications. The self-cleaning vibrating wire also utilizes profile wire technology for maximum strength, heavier loading and extreme open area. The design allows for significantly improved wear life, as the vibrating wire naturally absorbs and dissipates energy more efficiently than traditional systems. Steel Wire Screen
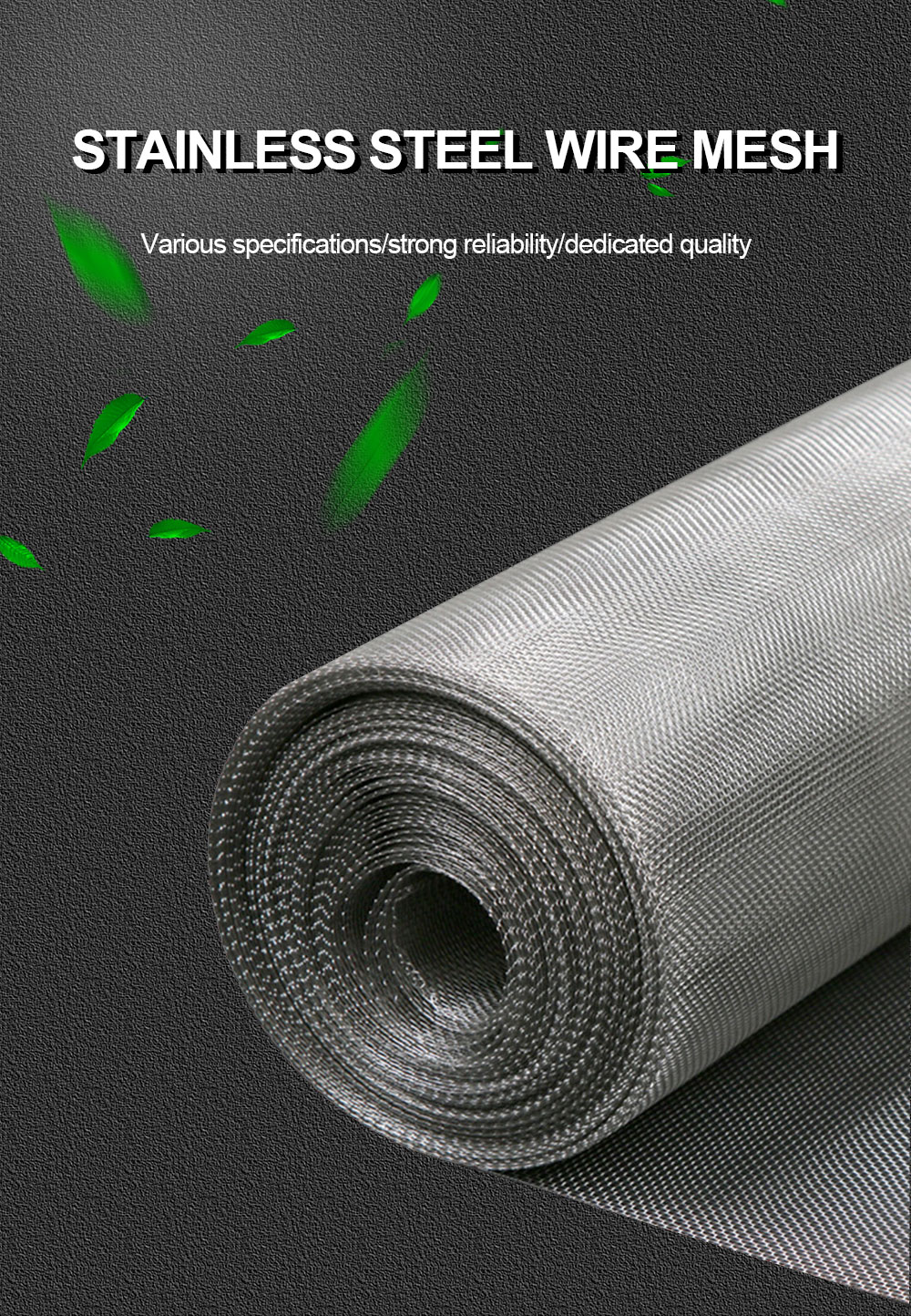
Rhino Hyde’s Rhino Grid cast urethane products aim to deliver superior wear properties across multiple screening lines. The products were tested in a number of applications, the company says, providing extended run time and reduced maintenance. Rhino Grid cast urethane has a higher capacity to resist rubbing or scraping during production, the company adds, outlasting materials such as rubber, plastics and metals and making it an ideal solution for high-impact or repeated impingement applications. The products are designed to reduce downtime and take the pressure off maintenance crews by lasting seven to 10 times longer than alternative applications, Rhino Hyde says. The products are available as side- or end-tension screens.
Metaldex Ultraclean is a Polydeck innovation engineered to drive maximum production results for aggregate operations. Polydeck says the product features key design upgrades from Metaldex VR, allowing it to deliver more effective cleaning and accurate sizing while providing a 3 percent increase in open area compared to similar modular wire products. Designed to push the boundaries of open area in modular wire products, the company says Metaldex Ultraclean is best used in dry, fine-sizing applications or when positioned at the discharge end of screen decks to eliminate blinding or plugging for increased efficiency.
Sharkskin is a screen media that combines the open area of woven wire cloth with the wear life of polyurethane. According to Hoyt Wire Cloth, Sharkskin’s design makes it light, flexible and easy to install. Sharkskin is a cost-effective solution for a variety of difficult applications, the company adds. The screens can be rolled and carried by one person. Other benefits are reduced near-size plugging and noise abatement. Hoyt says Sharkskin is ideal for smaller decks where open area loss won’t allow for the use of modular screen media.
Photo: Unified Screening & Crushing
Unified Screening & Crushing’s SuperFlow woven wire screen media helps producers achieve less downtime from screen changeouts, consistency in sizing, and lower costs per ton. SuperFlow, a self-cleaning screen with a combination of wire and urethane, offers flexibility and longer wear life, handles damp and sticky material, and greatly reduces plugging and blinding while maintaining accurate sizing, the company adds.
If you enjoyed this article, subscribe to Pit & Quarry to receive more articles just like it.
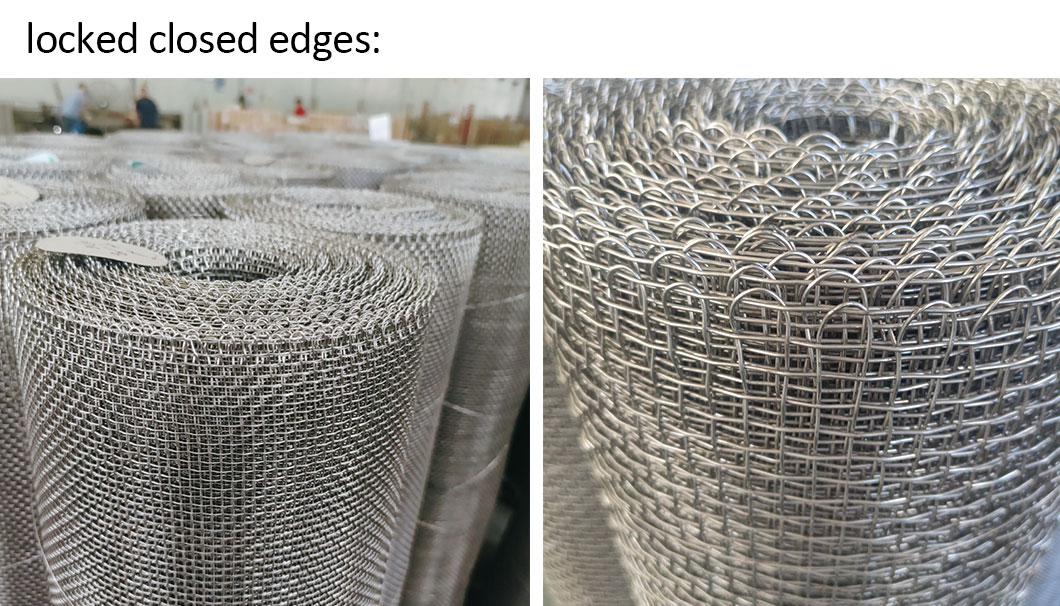
Steel Screen Net © 2023 North Coast Media LLC, All Rights Reserved.